引 言
静态混合器是由在光滑直管内装入不同形状混合元件构成的一种新型高效混合设备
[ 1] 。扭旋叶片是繁复多样的混合元件中的典型代表之一, 以扭旋叶片为混合元件的常见静态混合器有美*的 SK 型和日本的Hi 型等 ,这两种静态混合器在管内一个截面上分别安有一个和两个扭旋叶片
[ 2-3] , 由本课题组开发的一个截面上安有四个扭旋叶片的新型静态混合器已在环氧丙烷的工业生产中获得了成功应
用[ 4]
。
扭旋叶片的加入使混合管内流体的流动变得非常复杂,尤其是一个截面上安有多个扭旋叶片时, 从理论上寻求管内流场的解析解异常困难。计算流体力学的发展为采用数值模拟方法研究复杂流场提供了可能 ,近年来科研人员运用数值模拟方法对静态混合器中流体流动特性进行了大量研究, 在表明 CFD 是研究静态混合器流场特性的有效方法之一的同时也取得了许多成果
[ 5-11] 。但对以扭旋叶片为混合元件的静态混合器研究集中在 SK 型静态混合器上 ,对其他扭旋型静态混合器研究很少,互相间的性能比较研究更少 ,使得工程应用时对含扭旋叶片的静态混合器的选用更多的是依靠设计者的感觉和经验,缺乏可靠依据。
本文运用 FLUEN T 流体力学计算软件对含扭旋叶片的静态混合器内流场进行数值模拟计算, 从管内旋涡、湍动能、湍流强度及流体阻力等几方面研究扭旋叶片的组合对静态混合器流场特性的影响,为工程应用中扭旋型静态混合器的选用提供参考。为论述方便, 对一个截面上分别安有一**四个扭旋叶片的静态混合器分别称为单叶片静态混合器、双叶片组合、三叶片组合、四叶片组合静态混合器。
1 数值模拟
数值模拟计算采用湍流模型中常用的 RNGk-ε 模型 ,应用 FLUENT 三维单精度分离解算器 ,速度和压力的耦合采用 Simple 算法。求解流体流动控制方程可以表示为
[ 12] :
(ρt)+div(ρu )=div(Γgrad )+S (1)
式中 :ρ为流体密度 ; 为通用变量;Γ为广义扩散系数;S 为广义源项。
对不同扭旋叶片组合的静态混合器分别建立计算模型 :混合器内径为 100 mm ,管总长 1200 m m ,在混合器的入口处有一段 100 mm 长的空管段, 叶片厚为 2 mm , 单叶片静态混合器(即 SK 型静态混合器)的扭旋叶片规格 D ×L 为 100 mm ×200 m m ,混合器内装 5 个混合元件 ;对多叶片组合的静态混合器 ,考虑到叶片的安装, 扭旋叶片规格 D ×L 为 40 mm ×80 mm , 在同一截面的混合元件构成一组, 混合器内装 12 组混合元件。计算模型在 FLUENT 的前处理软件 GAMBIT 中进行网格划分,通常网格
划分越细 ,计算结果越精确,但计算量越大。本文采 |
件。从计算结果中提取的单叶片**四叶片组合静态 |
用四面体网格, 单叶片混合器模型共有 484119 个单 |
混合器研究截面的平面时均速度矢量图如图 2 所 |
元网格,双叶片组合混合器模型共有 483636 个单元 |
示 ,图中速度矢量为 |
|
x 与uy 的矢量叠加而不含 uz 。 |
u |
网格 ,三叶片组合混合器模型共有 492051 个单元网 |
|
|
|
|
格、四叶片组合静态混合器混合器模型共有 503789 |
|
|
|
|
个单元网格。图 1 为双叶片组合静态混合器中两组混合元件的网格模型示意图。
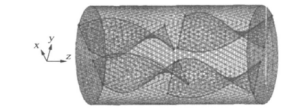
图 1 双叶片组合静态混合器网格划分示意图
Fig .1 Sketch of the mesh of the partial double screw static mixer
计算的入口边界条件为速度平均分布入口, 入口流速为 0.2 m/s ;出口边界条件为自由流出口 , 其他未设置的面默认为固壁无滑移光滑界面, 对近壁区采用标准壁面函数。模拟计算以水为流体介质 ,
其黏度 μ为 1.003 ×10
-3 Pa·s , 密度为 998.2 kg/
m
3 ,认为介质不可压缩 。
2 结果与分析
流场中任意一点的速度在湍流状态下是脉动的,通常用时均速度来表示这一点的运动速度 ,用与脉动速度相关的参数来表示流场湍流特性, 常用的表示参数有速度脉动均方根、湍流强度、湍动能及雷诺应力等
[ 13] 。
2.1 扭旋叶片的组合对管内旋涡的影响
分流作用方式与径向混合作用方式是扭旋叶片强化混合的两种主要方式
[ 2] , 混合器内径向混合主要靠管内旋涡形成。不同扭旋叶片组合引起管内旋涡也不相同。Hobbs 等的研究表明流体在混合元件入口和出口的流动受到元件交替的影响, 其影响范围达混合元件长度的 25 %以上
[ 14] , 又考虑到混合器入口和出口条件的影响, 故取各混合器中间段混合元件的中间截面作为研究对象来分析扭旋叶片的组合对管内旋涡的影响。
由于单叶片静态混合器扭旋叶片长度近似为多叶片组合静态混合器扭旋叶片的二倍, 故单叶片静态混合器取第三个混合元件、多叶片组合静态混合器取第六组混合元件作为各混合器中间段混合元
图 2 各混合器混合元件中间截面平面时均速度矢量图
Fig .2 Vector of time averaged velocity in the on center section
图 2(a)表明扭旋叶片两侧的流体近似于与叶片一起旋转 ,其旋向与叶片旋向相同 ,管内所有流体基本都参与这种旋转 , 旋涡半径近似等于混合管半径 ;图 2(b)中可明显观察到围绕两个叶片各自形成旋涡,旋向也与叶片旋向相同,旋涡半径近似等于叶片半径 ,比混合管半径的一半稍小,在没有叶片的两侧还有两个旋向与叶片旋向相反的旋涡 , 其旋涡半径也近似等于叶片半径;图 2(c)、2(d)表明在混合管内围绕扭旋叶片各自形成三个和四个旋向与叶片旋向相同、旋涡半径近似等于叶片半径的旋涡, 在三个和四个旋涡的空隙处各自还有三个和四个旋向与叶片旋向相反的旋涡 , 但旋涡半径均要小于叶片半径 ,且图 2(d)中这种旋涡半径比图 2(c)中这种旋涡半径更小。基于上述现象 ,可将混合管内的旋涡分为两种:一种旋涡是由叶片强迫其周围流体随叶片一起旋转而形成, 旋涡旋向与叶片旋向相同,旋涡半径不随叶片数量增加而减小 ,始终近似为叶片半径,可将这种旋涡称为强旋涡 ;另一种旋涡由流体在没有扭旋叶片作用的空隙处回流形成, 旋涡旋向与叶片旋向相反,它受到强旋涡的制约 , 扭旋叶片越多,没有扭旋叶片作用的空隙就越小, 这种旋涡的半径

· 86 · 北京化工大学学报 2008 年


就越小,可将这种旋涡称为弱旋涡。
流体在搅拌器中的流动可分为轴向流、径向流和切向流, 其中轴向流与径向流对混合起主要作用
[ 15] 。在多叶片组合静态混合器内分别有数量等于叶片数量的强旋涡和弱旋涡 , 且这两种旋向相反的旋涡交替排列 ,流体在混合器中心与器壁之间不断往复流动,使混合器内的径向流大大加强, 提高径向混合效果,从这点上看 ,一个截面上设置的扭旋叶片数量越多,其径向混合效果会越好。
2.2 扭旋叶片的组合对湍动能和湍流强度的影响
扭旋叶片的组合不仅会对管内旋涡产生影响 , 对管内流体的湍动也会产生影响。以 A(20 ,20)、B (30 , 30)两点为代表研究扭旋叶片的组合对管内湍动能与湍流强度的影响。
图 3 与图 4 分别为两代表点的湍动能和湍流强
度沿轴线变化图 , 图中 SK 、TWSK 、THSK 、FSK 分
别表示单叶片、双叶片组合、三叶片组合、四叶片组合静态混合器。从图 3 中可以看出 ,在每组元件的入口位置均有一个湍动能的尖峰 ,分析是由于流体从上一组混合元件流入下一组混合元件时, 元件的扭旋方向发生改变而引起的, 由于多叶片组合混合
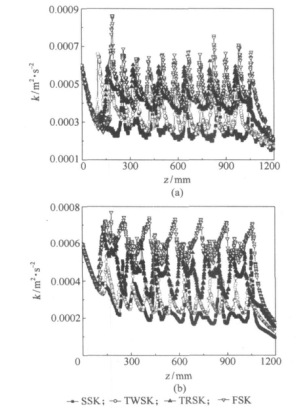
器内元件扭旋方向发生改变的次数多于单叶片混合器 ,其管内湍动能和湍流强度的尖峰数量也多于单叶片混合器。从尖峰的峰值上看 , 、四叶片组合混合器内的湍动能峰值**高 ,三叶片组合的其次,单叶片与双叶片组合的较低 , 分析是由于流体从上一组混合元件流入下一组混合元件时所有的旋涡都将被破坏 ,一个截面上扭旋叶片的数量越多 ,被破坏的旋涡数量就越多 , 流体的湍动程度越大, 湍动能也就越高。湍流强度与湍动能的情况基本相似。
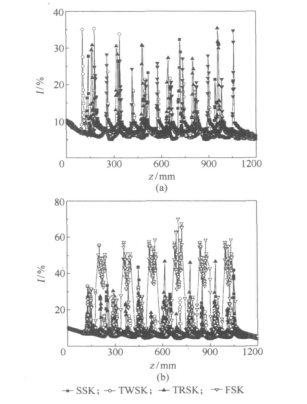
图 3 代表点湍动能沿轴线变化图
Fig .3 Turbulent kinetic energy at points along the z-axis
图 4 代表点湍流强度沿轴线变化图
Fig .4 Turbulence intensity at points along the z-axis
为更好比较各混合器内流体湍动程度, 定义代表点沿轴线的平均湍动能和平均湍流强度为:
|
|
z 2 |
|
|
|
=∫z1k(z)dz/(z 2 |
-z 1) |
k |
|
|
z |
(1) |
I |
=∫z12I(z)dz/(z 2 |
-z 1) |
式中 z 1 、z 2 分别为**个混合元件入口轴向坐标和**后一个混合元件出口轴向坐标, k(z )、I(z )分别表示代表点湍动能和湍流强度与 z 的关系函数。为便于计算结果处理, 将式(1)进行离散化表示为:

第 3 期 龚 斌等:扭旋叶片组合对静态混合器流场特性影响 · 87 ·

|
|
N |
|
也会产生影响。图 5 分别为两代表点沿轴线的压强 |
|
|
= ∑ k n(z )/ N |
|
变化图, 对多叶片组合混合器代表点压力降随截面 |
|
k |
|
1 |
(2) |
|
|
N |
上叶片的数量增加而增加 ,而单叶片混合器代表点 |
|
I = ∑ In(z)/ N |
|
|
|
压力降介于三叶片组合与四叶片组合混合器之间。 |
1 |
|
式中 N 为将代表点所在轴向直线在 z 1 ~ z 2 |
范围 |
为定量比较扭旋叶片组合对流体压力降的影 |
内离散的点数, kn(z)、In (z )分别为各离散点的湍 |
响 ,模拟计算了流速从 0.2 ~ 1.0 m/s 各混合器进出 |
动能和湍流强度。按式(2)得到单叶片、双叶片组 |
口压力差值即混合器压力降 ,计算结果入图 6 所示, |
合、三叶片组合、四叶片组合静态混合器内 A 、B 两 |
表明在同一流速下各混合器压力降由小到大顺序 |
点沿轴线的平均湍动能之比为 1∶1.30∶1.56∶1.75 ; |
为 双叶片组合 三叶片组合 单叶片 四叶片组合 |
, |
1∶1.09∶1.70∶2.25 , 平均湍流强度之比为 1∶1.18∶ |
: |
、 |
、 |
、 |
若单叶片混合器压力降为 1 , 则双叶片组合混合器 |
1.31∶1.41 ;1∶1.17∶1.38∶2.77 , 两代表点沿轴线的 |
压力降约为 0.51 ~ 0.54 ,三叶片组合混合器压力降 |
平均湍动能之比与平均湍流强度之比均表明随叶片 |
约为 0.78 ~ 0.81 , 四叶片组合混合器压力降约为 |
组合数量增加流体湍动程度呈递增趋势, 分析原因 |
1 15 |
1 18 |
|
|
|
|
|
|
|
. ~ |
. 。 |
|
|
|
如下 :一方面是由于一个截面上叶片的数量越多, 对流体的扰动程度越大 ,使流体的平均湍动程度加大 ; 另一方面是由于一个截面上叶片的数量越多, 在每组元件的入口位置引起的湍动尖峰越高, 也使流体的平均湍动程度加大。
2.3 扭旋叶片的组合对流体阻力的影响
混合管的流体阻力特性是也是混合管的重要性能参数之一 ,扭旋叶片的组合对混合管的流体阻力
图 5 代表点沿轴线的压强变化图
Fig .5 Pressure drop at points along the z-axis
图 6 各混合器流体阻力随流量变化图
Fig .6 Variation of flow resistance with flow velocity
3 结论
(1)单叶片静态混合器内仅有一个强旋涡, 而多叶片组合静态混合器内分别有数量等于叶片数量的强旋涡和弱旋涡, 且这两种旋向相反的旋涡交替排列,旋涡数量的增加有利于径向混合的强化。
(2)按单叶片 、双叶片组合 、三叶片组合、四叶片组合顺序静态混合器内湍动能与湍流强度呈递增趋势,表明一个截面上叶片的数量越多,对流体湍动的强化程度越大。
(3)在同一流速下按双叶片组合 、三叶片组合、单叶片、四叶片组合顺序各混合器流体阻力逐渐加大。